Porosity in Welding: Identifying Common Issues and Implementing Best Practices for Prevention
Porosity in welding is a pervasive concern that usually goes undetected up until it causes significant troubles with the stability of welds. This common defect can endanger the stamina and longevity of bonded structures, posturing safety and security dangers and leading to pricey rework. By comprehending the source of porosity and carrying out effective avoidance approaches, welders can substantially improve the top quality and dependability of their welds. In this discussion, we will certainly explore the vital elements adding to porosity formation, examine its destructive impacts on weld efficiency, and go over the most effective techniques that can be adopted to lessen porosity incident in welding processes.
Usual Reasons For Porosity

Another frequent perpetrator behind porosity is the visibility of impurities externally of the base steel, such as oil, oil, or corrosion. When these pollutants are not successfully eliminated prior to welding, they can vaporize and become trapped in the weld, causing flaws. Utilizing filthy or wet filler materials can introduce impurities right into the weld, adding to porosity problems. To reduce these common reasons for porosity, thorough cleansing of base steels, appropriate shielding gas option, and adherence to optimum welding criteria are crucial methods in accomplishing top quality, porosity-free welds.
Effect of Porosity on Weld Quality

The presence of porosity in welding can substantially endanger the structural stability and mechanical homes of bonded joints. Porosity creates voids within the weld metal, deteriorating its total strength and load-bearing capacity.
One of the main repercussions of porosity is a decline in the weld's see page ductility and toughness. Welds with high porosity levels tend to display lower effect toughness and lowered capacity to deform plastically before fracturing. This can be particularly concerning in applications where the welded components are subjected to dynamic or cyclic loading problems. Moreover, porosity can hamper the weld's capacity useful content to properly send pressures, bring about early weld failing and possible security dangers in important frameworks.
Finest Practices for Porosity Prevention
To enhance the structural stability and top quality of bonded joints, what specific steps can be carried out to decrease the occurrence of porosity during the welding process? Utilizing the proper welding strategy for the specific material being welded, such as adjusting the welding angle and gun setting, can additionally stop porosity. Normal examination of welds and immediate remediation of any issues determined during the welding process are vital methods to stop porosity and create top notch welds.
Value of Correct Welding Strategies
Carrying out correct welding strategies is extremely important in making certain the architectural honesty and high quality of welded joints, building on the foundation of effective porosity avoidance actions. Welding strategies directly impact the general strength and sturdiness of the welded framework. One vital element of index appropriate welding techniques is keeping the proper warm input. Extreme heat can cause increased porosity due to the entrapment of gases in the weld swimming pool. On the other hand, insufficient warmth might cause insufficient blend, creating prospective weak factors in the joint. In addition, making use of the appropriate welding criteria, such as voltage, present, and travel speed, is essential for accomplishing sound welds with marginal porosity.
Furthermore, the option of welding procedure, whether it be MIG, TIG, or stick welding, ought to straighten with the specific demands of the task to guarantee ideal outcomes. Proper cleansing and preparation of the base steel, along with selecting the ideal filler product, are additionally vital parts of proficient welding methods. By sticking to these ideal practices, welders can reduce the threat of porosity development and create top quality, structurally sound welds.
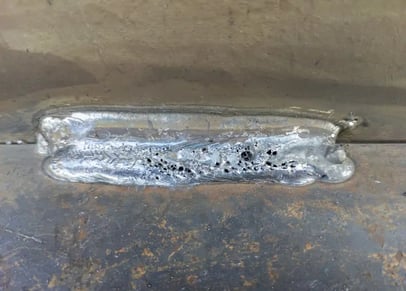
Evaluating and Quality Control Measures
Checking treatments are crucial to detect and protect against porosity in welding, ensuring the toughness and toughness of the last item. Non-destructive screening approaches such as ultrasonic screening, radiographic testing, and visual inspection are commonly employed to recognize prospective flaws like porosity.
Post-weld inspections, on the other hand, analyze the final weld for any type of issues, including porosity, and verify that it meets specified criteria. Executing a detailed top quality control plan that includes detailed testing procedures and assessments is extremely important to decreasing porosity problems and making certain the overall quality of welded joints.
Final Thought
To conclude, porosity in welding can be an usual issue that impacts the high quality of welds. By determining the usual sources of porosity and implementing best practices for prevention, such as appropriate welding methods and screening procedures, welders can make certain high quality and reputable welds. It is important to prioritize prevention methods to minimize the event of porosity and keep the honesty of bonded frameworks.